The amount of equipment and tight deadlines to which we are working requires a level of organization to which some graduate students may not be accustomed. We’ve implemented a manufacturing process adopted from the lean manufacturing world. The most important part in our process is the router document. This document lists top-level, step-by-step directions to completing an enclosure. In order to build a system, a router is printed for every enclosure involved. As a step is completed, the operator signs his or her initials and the date and time at which the step was completed. This router serves two major functions: one, to give the operator a list of instructions and two, to lend accountability and traceability to the build process. At the end of each day, each of us can take the routers we’ve worked on and upload to a shared document the latest step completed and the date and time at which it was completed. This will eventually allow us to see how much time it takes to build each system (hopefully over time this number will improve) and predict the completion dates.
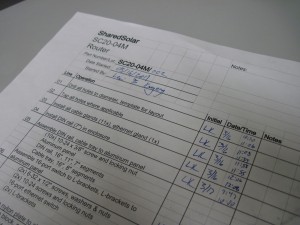
Another component of the process is what we’re calling a “construction document.†In industry, this type of information would be captured in a detailed engineering drawing, assembly drawing, or manufacturing drawing. Since we’re in the business of assembling off-the-shelf components into an enclosure and not building the components themselves, we thought the best way to capture the necessary technical information would be in a document. The construction document contains standard wire lengths, more detailed instructions, and photographs of the building process.
For these first couple systems, the routers have been beneficial in reminding us of the sequence of steps during the process. We hope that further into the big build, they will be more valuable in tracking time-to-build and estimating ship dates.
Here’s the first mass-produced metering enclosure!
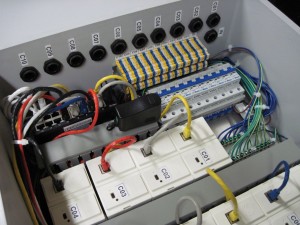